Welcome to Foshan Pinshang Machinery Co, Ltd.
Service Hotline:
+86 13791266555
06
2024
-
06
How to choose and maintain anilox rollers for flexo printer
Category:
Anilox roller is a very fine and important part of flexo printer transfer part, what is the role of specific anilox roller? What are the parameters of anilox roller? And how to use and maintain anilox roller?
First, the structure and types of anilox rollers
From the anilox roll surface structure, mainly by the net hole and the net wall of two parts; from the anilox roll structure, mainly by the core, base material and surface plating. The commonly used base material is electroplated copper, which is the basis for making anilox roll mesh cavities and mesh walls; the surface plating layer is made of metal chromium or ceramic, which is mainly used to improve the wear resistance of anilox rolls and block the corrosion of solvent on the base layer of copper.
According to the different anilox surface plating can be divided into metal chrome anilox and ceramic anilox, from the engraving accuracy, print resistance, ink transfer and release performance comparison, due to the ceramic anilox has more advantages, so the enterprise is more use of ceramic anilox.
Metal anilox roller processing technology flow: metal roller base → copper plating → engraving → chrome plating
Ceramic anilox roller processing technology flow: metal roller base→copper plating→engraving→sandblasting treatment→ceramic material coating→polishing
Metal roller base→coated ceramic material→polishing→laser engraving
Because the first engraving after chrome plating or spraying ceramic will lead to the reduction of anilox volume, and the first spraying ceramic and then laser engraving method can ensure the anilox precision, which is also one of the reasons why ceramic anilox rollers are more widely used.
Second, describe the parameters of anilox roller
The role of anilox roller is to the printing plate graphic part of the quantitative and uniform transfer of ink. Whether the anilox roller can quantitatively, uniformly and accurately pass the ink directly depends on the parameters of the anilox roller.
1. Anilox shape
Anilox shape has four-pronged cone, four-pronged platform, six-pronged platform, spiral and so on. At present, most of the four-pronged cone-shaped aniloxes exist on metal anilox rollers, which are completed by electronic engraving technology; most of the six-pronged table-shaped aniloxes exist on ceramic anilox rollers, which are made by laser engraving, and compared with four-pronged cone-shaped aniloxes, they have the features of storing more ink and having better performance of transferring ink and releasing ink.
2. Number of anilox lines
The number of anilox lines is different from the number of dot lines, which is defined along the anilox roller axial direction within the unit length of the number of net holes, the unit is line / inch or line / cm. The number of anilox lines is different from the number of dot lines in another point is that the number of anilox lines and the clarity of the printed graphic does not have a direct correlation, but affects the quality of the printed graphic.
3. Anilox angle
Produced using electronic engraving anilox roll because of the different angles of the engraving knife, respectively, can be carved out of 30 o, 45 o, 60 o of the mesh point, laser engraving is usually carved out of 60 o positive six deformation of the mesh point.
4. Mesh opening, depth, opening degree
Mesh opening refers to the width of the opening on the surface of the mesh cavity, usually expressed in b; mesh depth refers to the depth of the mesh cavity, usually expressed in H; mesh opening refers to the depth of the mesh cavity (H) and the percentage of the opening of the mesh cavity (b), usually between 23% and 33%, the best in 28%.
5. Anilox volume
Anilox volume refers to the anilox roller unit surface area can accommodate the total amount of ink, the unit is BCM/in2 (B-Billion; C-Cubic; M-Micro). It is a parameter that reflects the size of the ink storage capacity of the anilox roller, converted to domestic units, 1BCM/in2 = 1.55cm3/m2.
Third, anilox roller use factors to consider
1. Select the appropriate anilox volume
The size of the volume directly determines the size of the anilox roller's ink supply, different fineness of the prints need different ink supply, so the anilox roller should be selected with full consideration of the anilox volume.
2. Select the appropriate number of anilox lines
Generally speaking, anilox roller ink supply with the increase of anilox lines and decline, the higher the number of anilox lines, the smaller the ink supply, the better the relative uniformity. For a single anilox, the shape of the anilox determines the existence of corners inside the anilox, and it is also because of the existence of the corners of the anilox that causes the obstruction of the anilox to the ink transfer, i.e., the “corner effect”. The higher the number of anilox lines, the more the number of mesh holes per unit length, taking into account the existence of the mesh wall between each two mesh holes, so in the case of the same volume, the higher the number of anilox lines, the greater the opening of the mesh holes, i.e., the greater the relative depth of the edge effect is also more serious, which results in a reduction in the amount of ink transfer. Therefore, when choosing the number of anilox lines, the ink supply should also be fully considered.
①Consider the fineness of the printed matter
Relatively speaking, the field, lines, text, etc. require a large amount of ink, select the anilox line number to choose a lower; color anilox pattern requires a small amount of ink, select the anilox line number is higher (as shown in Table 1). In addition to the factor of ink supply, at the same time to consider the number of dots on the printing plate line. The fineness of the printed matter depends on the dot line number of high and low, on the printing plate, the dot size is determined, if a lower line number of anilox rollers, at this time, the area of each anilox will be larger than the area of certain dots on the printing plate, so that when printing, the dots as a result of the lack of support from the bulkheads, the dots will be immersed in the anilox, not only the surface of the dots are inked, but also the sidewalls will be inked, which leads to the dots to increase, for example, for the 80% dot area rate size of the color block will lead to paste dead, printing into the field, while leading to edge ghosting failure. Practice has shown that to obtain superior quality printing, anilox roller anilox lines and the number of dot lines of the printing plate to maintain a better ratio of about 4:1.
② Consider the substrate material and printing requirements
Different substrate materials with different ink absorption, different substrate materials with different ways of ink drying, so it should be fully taken into account the substrate material demand for ink factors, general ink absorption, select the anilox line number of low, small ink absorption, select the anilox line number of high.
3. Select the appropriate shape of the mesh
①Compatible with the ink supply form
Flexographic printing ink supply form is mainly divided into two types of double roller and scraper type, which can be divided into positive scraper, reverse scraper, fully enclosed double scraper three. In the same number of lines under the conditions of the four-pronged conical mesh cavity volume will be due to the doctor blade wear and rapid reduction, therefore, four-pronged conical mesh cavity with the majority of cases with the double-roller ink supply form use. While four-pronged platform, six-pronged platform can be applied to the scraper type.
②Compatibility with Ink Type
The slanting line shaped anilox can ensure the fluidity of the ink and improve the ink transmission of anilox rollers. So for the ink with high viscosity, or varnish, coating, etc., the slanting anilox roller can be used for ink supply.
4. Select the appropriate anilox angle
Usually, in most cases, choose 60o, hexagonal ceramic anilox rollers for ink supply, only in special cases using other angle anilox rollers.
In addition to the above factors, but also fully integrated with the actual needs of enterprises to choose which type of anilox roller is more appropriate, such as from the enterprise cost considerations.
Maintenance of anilox roller
Anilox roller is the most precise part of flexographic printing machine, pay attention to the daily use of the maintenance process is to extend the service life of anilox roller is an important part.
1. Use the anilox roller protective cover when storing the anilox roller.
The use of anilox roller protection sleeve, on the one hand, play a better role in buffer vibration absorption, on the other hand, can be very good to keep the anilox roller surface clean.
2. Test the ink viscosity and clean the anilox in time.
The reason of anilox clogging, on one hand, is the nature of the ink itself, such as drying too fast; on the other hand, is the reason of cleaning, such as cleaning is not thorough or cleaning is not timely. Therefore, the printing process should pay attention to keep the viscosity of the ink constant, anilox roller cleaning, as far as possible to use the anilox roller damage less cleaning methods and timely cleaning is crucial.
3. Using high-quality doctor blade and magnetic filter
Use high-quality doctor blade, and control the pressure between the doctor blade and anilox roller, under the conditions of the conditions allow, in the ink tank into the magnetic filter, thus reducing the impurity particles in the ink, reduce the wear and tear of the anilox roller, prolong its service life.
4. Use the mesh microscope to regularly check the net hole
Use an anilox microscope to check the anilox regularly, and take timely measures to deal with the problems such as scratches and blockage of the anilox roller.
Related News

Service TEL:
+86 13791266555

Add:
No. 61B, Anhua Road, Fuwan Town, Hecheng Street, Gaoming District, Foshan City, Guangdong Province, China
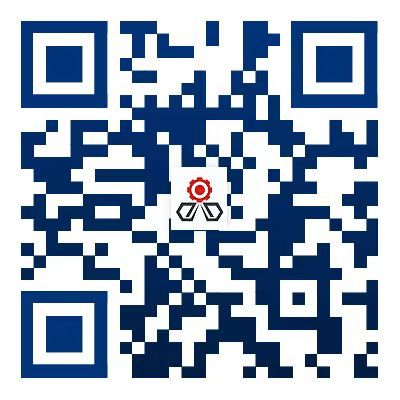